As a manufacturer of plastic packaging, do you want to make products from PET in the future or are you generally interested in possible alternatives to PP? Then you should plan a visit to Netstal at the NPE. In Orlando, we and our system partners will be demonstrating what sustainable and recyclable thin-wall packaging can look like. At our stand W223, we will be producing a thin-wall cup made of 100% PET on a hybrid Elion 3200. The transparent cup can be processed together with empty PET bottles into high-quality recyclates.
The recycling rate for thin-walled plastic packaging, such as cups for dairy products or spreads, is still low worldwide. This contrasts with PET bottles, which play a pioneering role in recycling. Across Europe, half of all PET bottles placed on the market were already recycled in 2020. The trend is also rising worldwide. However, if all types of PET packaging are considered, the rate is still 35% (source: Statista). Due to its good recyclability and the established recycling systems in several countries, the idea of using PET for thin-walled packaging and making it specifically recyclable is an obvious one. PET packaging must meet certain criteria so that it can be easily collected via the established collection systems and processed into rPET regranulate in the recycling plants together with PET bottles. This is an important prerequisite so that new bottles and packaging can be created from all PET containers.
"Clear packaging or the absence of color additives is preferred for PET packaging in order to achieve the purest possible quality of rPET. At the NPE, we will be showing such a PET cup that is optimized for recycling."
Reto Gmür, Produktmanager Packaging
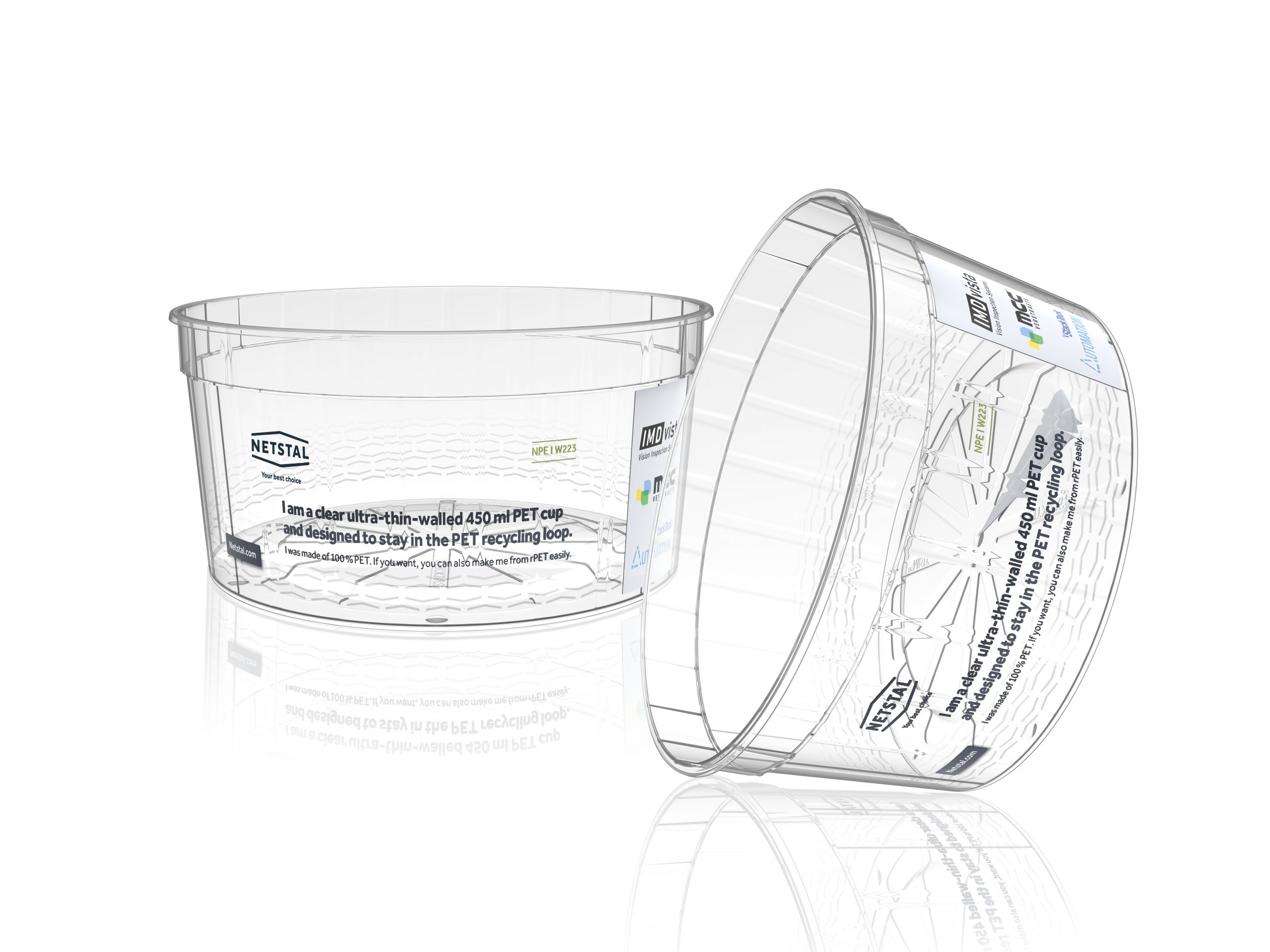
The thin-walled PET cup weighs around 15 g
Sustainable PET thin-wall cup produced in a climate-friendly way
We have developed such a recycling-optimized solution for the NPE and in collaboration with our system partners. The clear cup weighs around 15 g and has a filling volume of 450 ml. We process virgin PET from the Eastman Chemical Company. We put the cups into the NPE recycling program so that the material remains in the PET cycle without loss. The labels are also made of PET and are provided by the Belgian IML specialist Verstraete. Our Canadian partner StackTeck provides the test mold with two cavities as well as the IML robot that inserts the labels into the cavities and removes and stacks the finished cups.
The PET cup is injection molded in a cycle time of around 4 seconds on our Elion 3200. With its electric toggle clamping unit and hybrid injection unit, the injection molding machine delivers the necessary speed, performance and dynamics. By recuperating kinetic energy from the clamping unit, the Elion is one of the most energy-efficient injection molding machines on the market. In high-speed applications, the Elion is in efficiency class 8 and higher of the latest Euromap 60.1 standard. The unit with RFC injection control shines with its leading shot-to-shot consistency. This is only available from Netstal in this form: The force-dependent pressure changeover is independent of the material properties and enables our customers to keep the part weight within tight tolerances at all times. You do not pay any extra for the leading Netstal precision, because the highest precision has been standard at Netstal for decades.
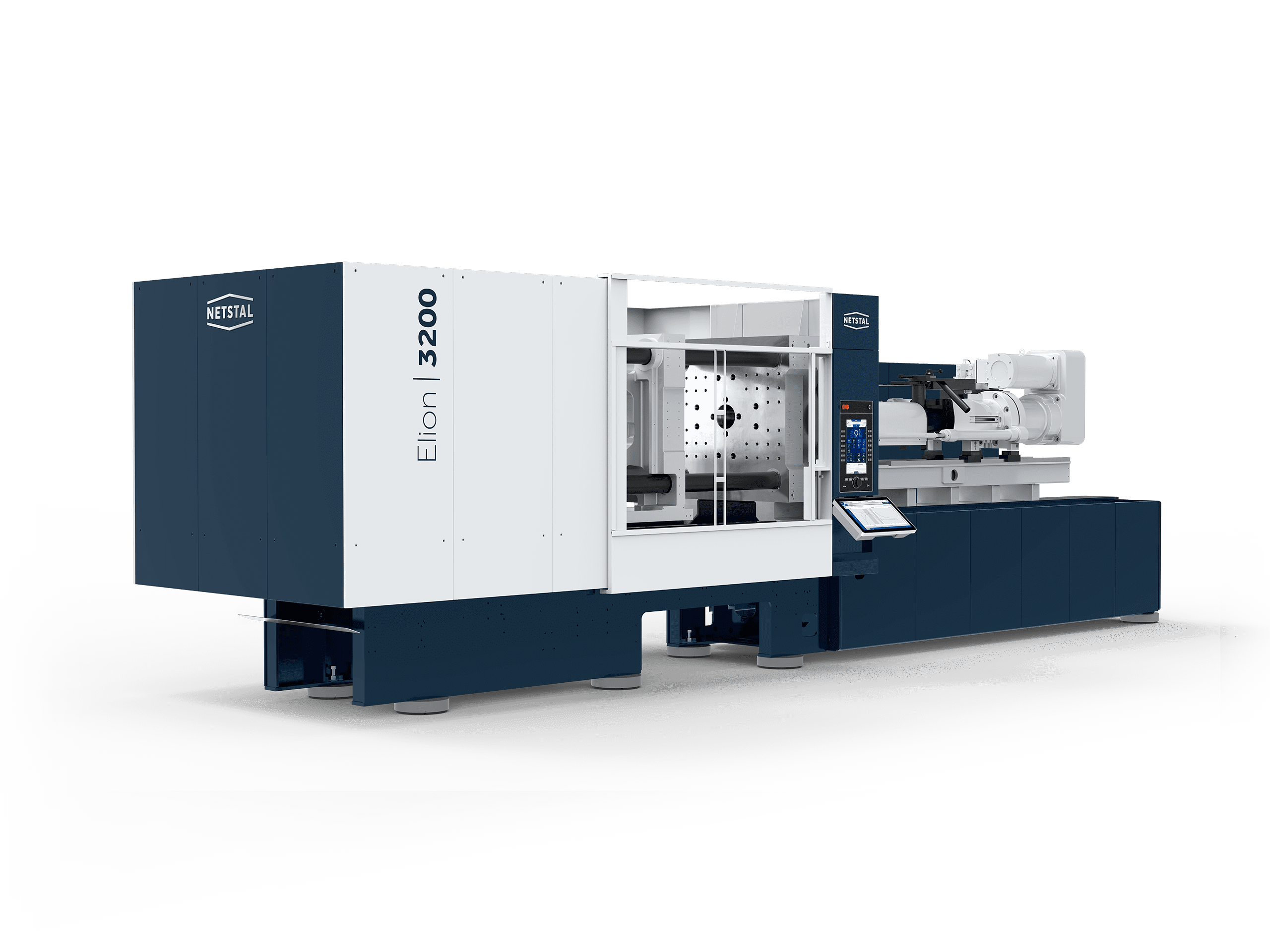
High-performance and energy-efficient injection molding machine: the Elion 3200
The Elion 3200 is equipped with the optional adaptive pressure reduction. This optional function helps you to save energy. If the pressure reduction is activated, the hydraulic system pressure is permanently adjusted to the optimum point. This option offers you enormous advantages. With a lower pressure, the axles of the machine are less heavily loaded. This has a positive effect on availability. However, the main benefit is the further reduction in power consumption. You produce particularly efficiently and at the lowest unit costs.