Greater efficiency and productivity can also be achieved with existing machines. With Smart Operation, we offer you an innovative solution for optimizing operating processes in injection moulding production. Retrofitting is possible for all Netstal machines from control system generation Axos 7.
In high-performance applications, the aim is often to keep reducing cycle times in order to be able to produce even more. However, sometimes these gains are eaten up by small efficiency losses. This means that non-technical downtimes are either not taken into account or are regarded as unavoidable. With Smart Operation, you can reliably eliminate such downtimes and increase productivity.
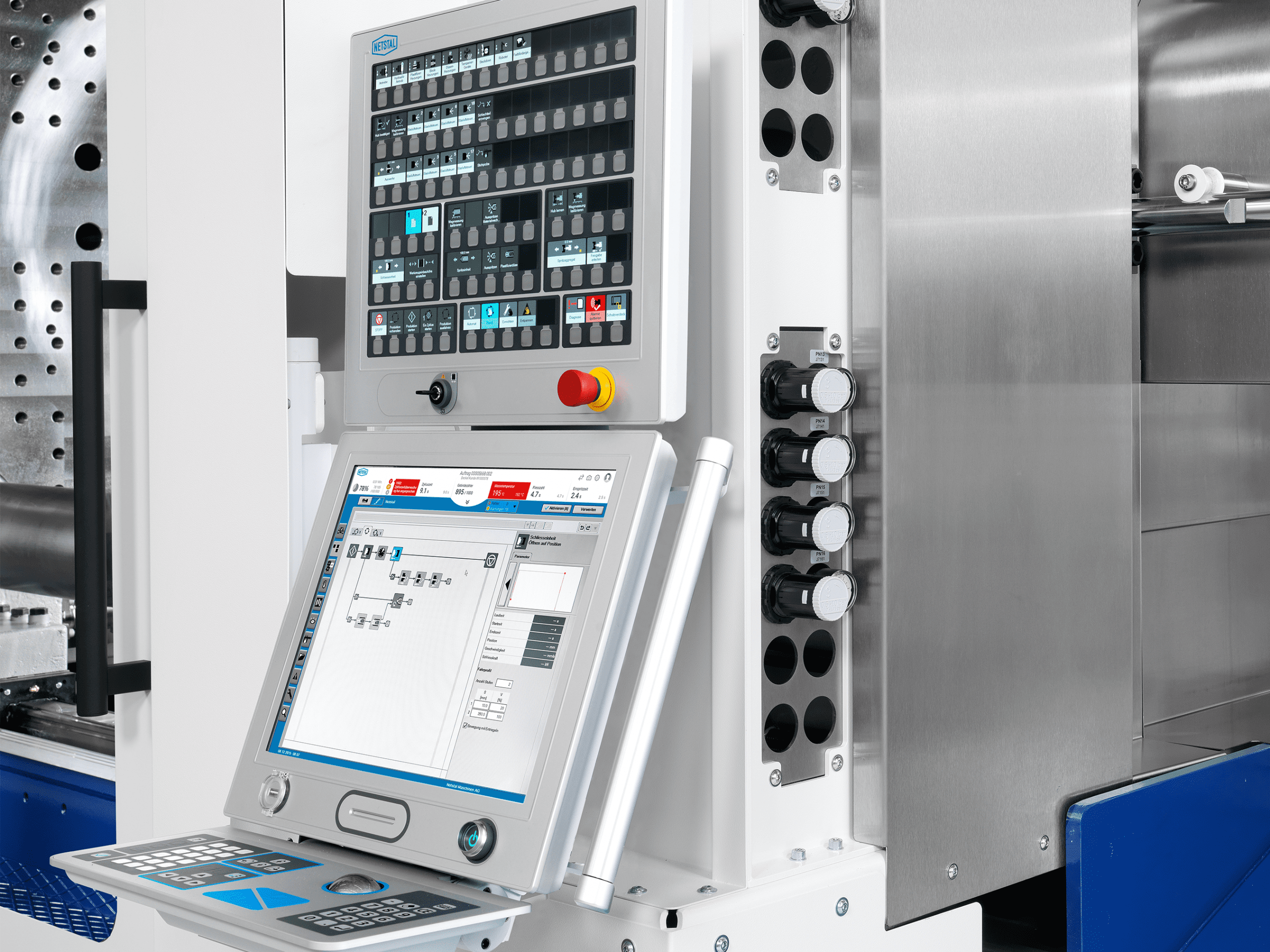
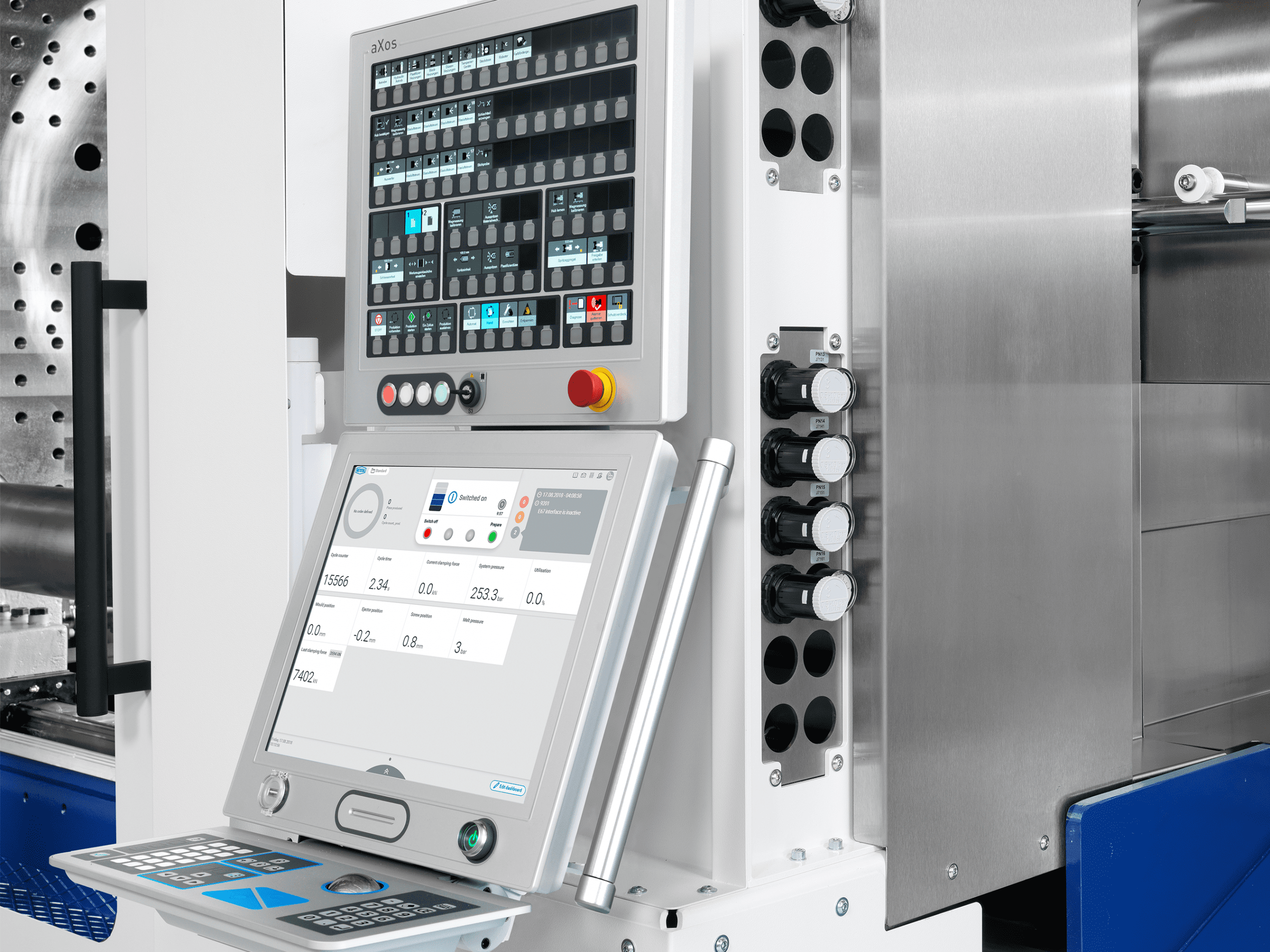
More efficiency can be retrofitted: After the conversion, the Axos control unit has 4 additional Smart Buttons and a software update
(Move the slider to the left to see the controller after the conversion)
Sales increase in the six-figure range
A customer example: In the production of dental components, the injection molding machines have to be stopped at regular intervals in order to lubricate the tools. As the plant maintenance staff are unable to operate the injection molding machine, specialist personnel have to be called in each time. As the specialist has to look after several systems at the same time, there are always waiting times of several minutes. However, this adds up over the year and the negative impact on productivity is significant.
With Smart Operation, we were able to offer this customer an optimal solution. By anchoring specific production processes in the machine control system, a guided operation was created that can also be carried out error-free by maintenance personnel after a short briefing. Today, this customer has equipped several machines with Smart Operation and reports a six-figure increase in turnover. This is solely due to the elimination of the many short waiting times. Today, the plant maintenance staff independently access the machine, stop production, lubricate the tool and then restore the entire production cell, including the removal robot and packaging system, to production status.
Intuitive and safe operating concept eliminates non-technical downtime
The Smart Operation concept is based on anchoring operation-relevant scenarios and processes in the control system and changing the operating status at the touch of a button. A total of 4 of the so-called “Smart Buttons” are available. A color code on the main screen clearly indicates which buttons can be used to continue. The relevant buttons light up in the corresponding colors. For example, red for “Stop cycle mode” or green for “Start cycle mode”. If certain work steps are also required, such as ejecting the injection unit, this is displayed as an instruction. The execution must be confirmed before the next step can be continued. The principle is as intuitive as operating a coffee machine that indicates when the coffee grounds container needs to be emptied or a descaling program needs to be carried out.
Another application scenario is the rapid rectification of faults during the night shift. With Smart Operation, most faults can be rectified immediately by shift personnel. There is no need to wait until an application engineer arrives.
Users of Smart Operation benefit in several ways: the implementation of clearly defined processes protects capital goods from improper operation and reduces the risk of operating errors. Repair costs are reduced and system availability increases. Situational user interactions drastically reduce the amount of training required. Instructions printed on paper are no longer necessary. Smart Operation significantly increases overall production efficiency.
We always recommend adding Smart Operation for new machines. Smart Operation can be retrofitted to existing machines with Axos 7 and Axos 8 at any time. We will be happy to provide you with an efficiency consultation for optimum operating processes with Smart Operation and prepare a retrofit offer tailored to your needs.
Go to LinkedIn to read the Success Story with SFS from the year 2022: