The Netstal brand has always stood for high performance but also for maximum precision and reproducibility. The demands from the industry on the quality and consistency of the produced components are constantly increasing. The unique and highly accurate RFC injection control system from Netstal plays a decisive role precisely in this context. Thanks to stable mechanical construction, highly accurate measurement technology and sophisticated control technology, the injection units from Netstal achieve an extremely high shot weight consistency. This means that the user can fully rely on his production.
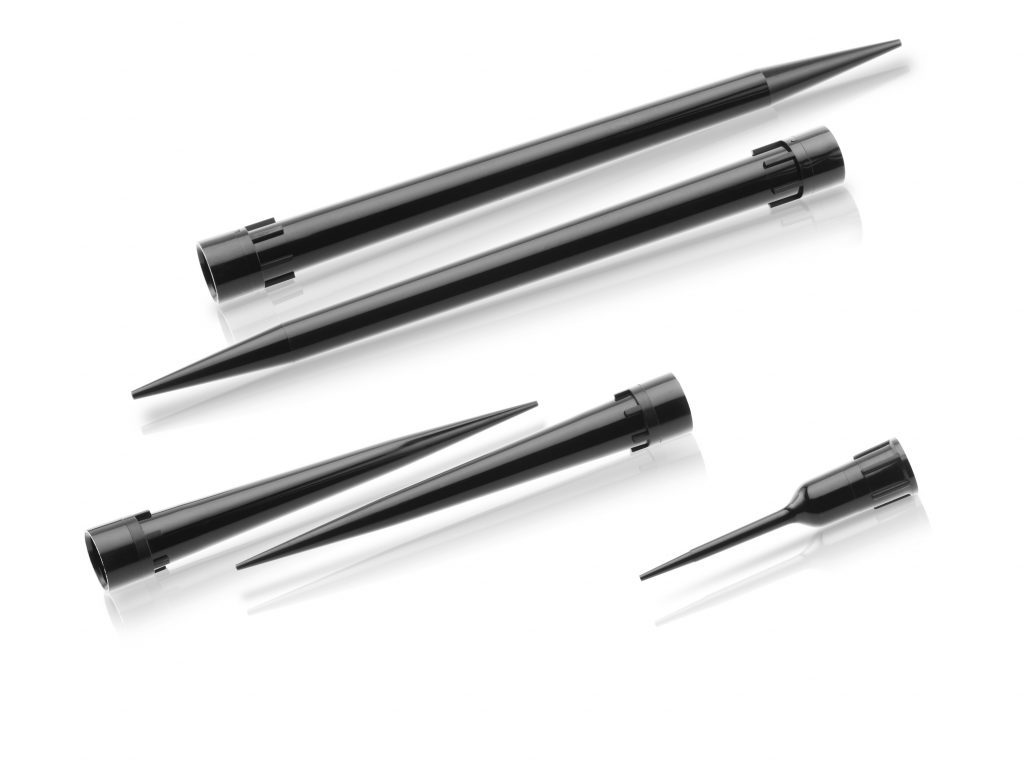
In addition to the high demands on precision and reproducibility, productivity is constantly increasing. Cycle times are decreasing and the number of cavities is increasing. An example of this is the production of pipette tips. Today, high-performance systems produce on 64-cavity molds with a cycle time of less than 5s.Netstal already proved at the K show 2016 that 128 cavities are also possible:https://www.youtube.com/watch?v=fZ19sM7-KQw&ab_channel=NetstalIn terms of quality and reproducibility, the control of the injection process plays a central role. Already when filling the cavities, it is decided whether the parts will be within the set tolerance or not.The developers at Netstal are aware of this fact and have always placed a strong focus on injection control. From the machine’s point of view, the control quality of the injection process is based on the following three features:
- Stable design and the most direct power transmission possible from the drive to the screw tip
- Highly sensitive sensors and high sampling rates
- Powerful control algorithms and real-time capable computer systems
Netstal RFC (responsive filling control)
The control of the injection process includes two phases:
- Injection phase
- Holding pressure phase
During the injection phase, the injection speed is tracked as the leading controlled variable. During this phase, the specified velocity profile is readjusted as accurately as possible and without delay. This can be seen clearly in the following screenshot in the diagram on the left.
Diagram: Injection phase (left) and holding pressure phase (right)
As soon as the cavities are filled volumetrically, the controller switches to the holding pressure phase and here the injection force is tracked as the leading controlled variable. This can be seen in the right diagram of the screenshot above.
The decisive factor is now how and at which screw position the switchover from speed to pressure control takes place. This is commonly referred to as v/P changeover.
Displacement or pressure dependent?
In practice, changeover is usually position-dependent. This means that the changeover takes place at a certain screw position, irrespective of the current quality of the melt. Due to various external influences, the melt quality can be subject to fluctuations, which are subsequently reflected in a greater scattering of the shot weight and thus of the component quality.
However, pressure-dependent changeover is particularly advantageous, especially for short injection times and fast cycles. Here, the changeover process is determined by the melt pressure. This strategy has the advantage that fluctuations in melt quality are automatically compensated. This leads to a higher shot weight consistency and thus to better quality reproducibility.
The pressure-based v/P switchover RFC detects very precisely when the mold cavities are filled volumetrically and the optimum time for initiating the holding pressure phase has been reached. This leads to a high shot weight consistency by automatically compensating for external environmental influences such as material fluctuations and the closing behavior of the non-return valve.
The role of the non-return valve
As a mechanical element at the screw tip, the non-return valve plays an important role in the injection process. Its correct function is a mandatory prerequisite for a controlled and cleanly controllable injection process. On the one hand, it must be ensured that the non-return valve seals well when closed and that no disturbing leakage losses occur, and on the other hand, the closing behavior is also of great importance. For these reasons, regular inspection and maintenance of the non-return valve is highly recommended.
To positively influence the closing behavior, the highly flexible functionality of the aXos control system can be used. Namely, if the metering process is designed in such a way that the back pressure is maintained at the end of the metering time, the non-return valve is actively closed after metering. The subsequent injection process can then already be started with the non-return valve closed, which further improves shot weight consistency. As of control version aXos 8.5.1, the user is additionally supported in this setting with a new synchronization mechanism, which significantly simplifies the setting process.
The result can be measured.
The precision and reproducibility can be demonstrated using the example of a test series on the “Connector” component.
Diagram: Measurement series “Connector”
The diameter b was measured for 200 consecutive cycles. The mean value of the measurements was 18.499mm. The values scattered minimally by 0.008mm which, with the set tolerance of 18.5 +/- 0.0.1 mm, results in an excellent CpK value of 1.96 .
Quality through process reliability
Achieving high and, above all, consistent quality requires that the production process is 100% under control. The production system must be able to compensate for external influencing factors and ensure a sufficiently large process window with the available performance. Netstal machines provide the basic prerequisites for this right from the start: Stable construction, high-precision sensor technology and sophisticated control technology.
So when it comes to high-precision and reproducible production, it pays to choose Netstal.