With adaptive system pressure reduction, we presented a retrofittable option in 2023 that allows manufacturers to effectively save energy costs. The potential varies depending on the application.
Initial situation:
Using a coffee cup, we wanted to find out whether the calculated savings can be confirmed in practice. The thin-walled cup is produced in a 6-cavity mold on an Elion 2800 with a cycle time of 3.9 seconds. The shot weight is 95 g.
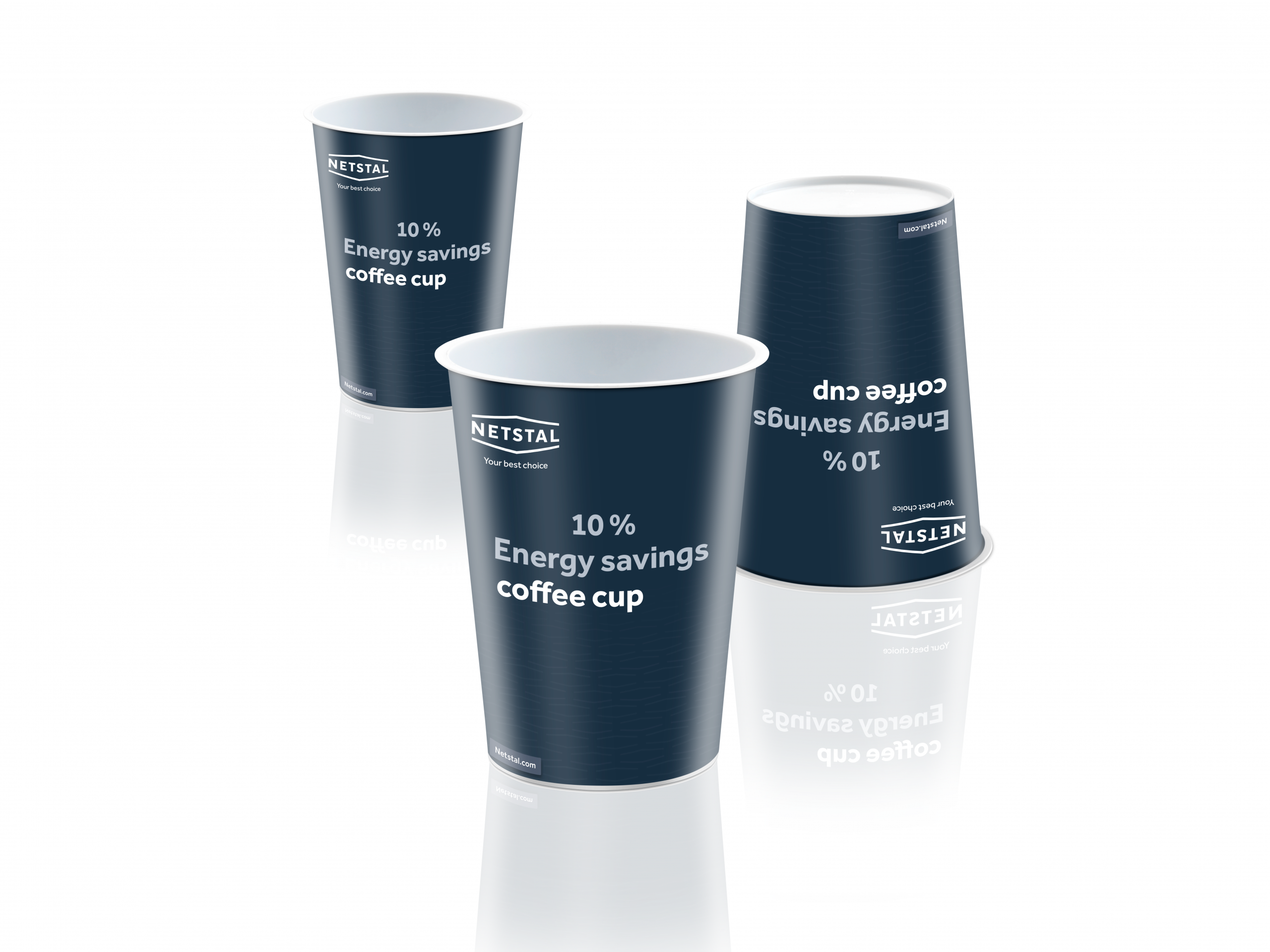
Solution from Netstal:
The application described was tested extensively with activated system pressure reduction. With the option activated, the injection molding machine requires around 10.5% less energy. A considerable reduction in costs and a relevant reduction in the CO2 footprint.
Calculate your individual savings potential:
With our new online tool, you can find out immediately whether you have a savings potential in your application with the adaptive system pressure reduction from Netstal and how high this is. Click on the link and enter the basic data on the machine and the current injection molding process. You will immediately receive a result.
Adaptive system pressure reduction
The hydraulic system of Netstal injection molding machines is designed for a maximum operating pressure of 250 bar in order to be able to cope with peak loads without any problems. Depending on the application, a lower value would also be sufficient. This is where Netstal comes in with the new system pressure reduction and optimizes energy efficiency. In automatic mode, the adaptive control system determines the optimum point at all times and adjusts the system pressure accordingly. With the same or even increased productivity, the energy consumption for providing the system pressure is reduced to a minimum. A lower load on the components also has a positive effect on machine availability and overall service life.